Analysis
Unfortunately Redbull did not schedule any Flugtag competitions this year so we were not able to test our design. Our plan was to build a full scale model for the Expo but because of the COVID-19 outbreak we were forced to pause our construction progress. Below is an analysis of our design which includes lift generated, predicted distance travelled and stress analysis of our wing frame.
​
For the analysis we decided to use two different sizes of our main wing. One is having our main wings be 8 feet wide and 8 feet long and the other example is a smaller wing of 8 feet wide and 4 feet long.
​
Also we tested two different speeds of 10 mph and 15 mph. We believe we could push our cart to 10 mph and 15 is an extreme case where we all got in amazing shape and obtained a faster takeoff speed.
Calculating Weight
The chart on the right shows how we calculated all of the components that make up the total weight of the glider in flight.


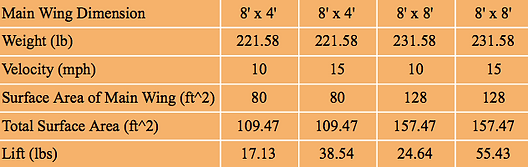
Calculating Lift
First semester we tried to simulate our full 3D model in a fluid dynamic software and it took 3 days to run and didnt provide any helpful results.
​
Here we used a general lift equation that calculates lift using Air Density, Speed, and Surface Area.
​
We now can solve for estimated distance travelled
Distance Projections
Using the lift we calculated above we were able to estimate the distance travelled for each situation for our Flugtag. It is important to note that this calculation was performed under idealized conditions and does not take in to account any drag or change in horizontal velocity.
​



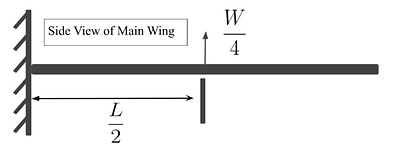

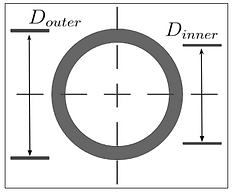
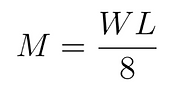




Stress Analysis
We wanted to calculate the yield stress in the most critical element of our design and that is the bending moment in the pipe and it is located in the middle where it passes through the wooden I-Beam.
​
First we have to solve for the moment which is usually caused by the weight due to gravity but since it is in free fall we use the lift generated by the wings and substitute Lift in our moment equation as W.
​
Next we solve for the moment of inertia of the cross section of the pipe using the equation show to the left.
​
Finally we use the stress equation and use the outer radius as c to find the bending stress.
​
Comparing different materials and sizes we can see that PVC would not hold up.
​
In our final design we use two different sized aluminum pipes in order to make our wings detachable. This analysis shows that the larger pipe with a diameter of 1' at our estimated speed of 10 mph will have a lower bending stress than the material's yield stress greater than our desired factor of safety of 1.5 from our standards.
Computational Fluid Dynamics
To better understand and optimize the aerodynamic properties of our craft design, we utilized computational fluid dynamics (CFD) software. We were able to run a basic, preliminary test in SimScale, but further tests were halted due to complications with mesh generation. This test gave us some useful insight, but we still intended to rerun it either in COMSOL or SimScale for more accurate results. However, due to time restrictions and some shifts in focus, we decided it to be less necessary than other components of the project. Since it no longer contributed significantly to defining success for this project, further analysis was cut. The images shown display the pressure and velocity data of one of our earlier designs, gathered from the preliminary test run.
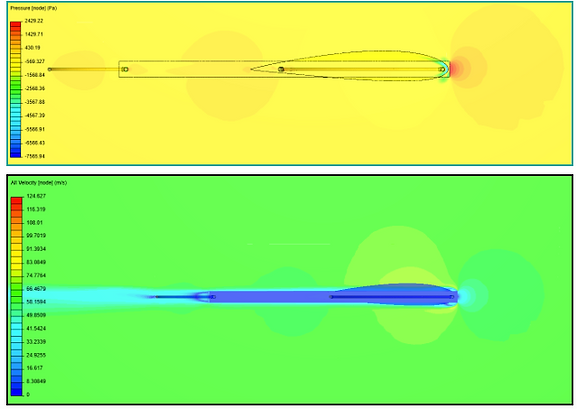